
Cost estimation can be challenging for buyers due to the highly diverse prices in manufacturing industries. Some software companies offer add-on applications that work with CAD files to calculate manufacturing costs using algorithms. Some software also integrates with online AI models to fetch instant prices for raw materials, labor costs, machining, post-processing, and more. However, all these applications still require some time to be fully adopted by the industry.
For accurate cost estimation and price comparison, it’s essential to understand the factors that influence costs. Here, we mention three key factors, though there are many more.
1. Material Selection Matters Most
To make a consistent cost estimation, we need to understand the material being used. If we select materials that are widely available in the market, estimating the cost of our raw material needs becomes easier. Choosing rare materials makes it harder to find accurate price information. Even if you know the current price of a rare material, it may fluctuate weekly. Thus, material selection is the foremost factor in ensuring consistency in cost estimation.
For example, the following alloys are commonly available:
Aluminum alloys: 60xx, 50xx, 70xx series
Stainless steels: 1.4301 (304), 1.4401 (316)
Structural & Carbon steels: C40, 42CrMo4, S235 (ST37), S355 (ST52)
Brass alloys: MS58, H59
2. Quantity of Your Need
The reliability of cost estimation is closely tied to the quantity of the product to be produced. Higher quantities allow for more accurate cost breakdowns. It’s important to note that engineering work is required regardless of whether the order quantity is 1 or 100, and the engineering cost remains constant. As the order quantity increases, the proportion of engineering costs—often the least predictable part of the price—decreases relative to the total cost. This makes the total cost more predictable as the quantity increases, leading to a more reliable cost estimation.
For example, when producing a stainless steel DN10 flange using CNC turning and milling machines, the ratio of engineering cost over unit price varies significantly between small and large quantities.
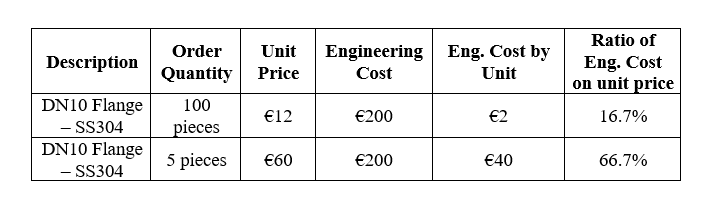
*Please contact us for your stainless steel flange needs. The prices listed are for reference only.
Creating an accurate cost estimate is particularly challenging for prototype manufacturing. Buyers may decide based on comparisons with available RFQ (Request for Quotation) returns rather than conducting a detailed internal cost estimation.
3. Location of the Manufacturer
The physical distance between the manufacturer and the buyer is crucial for making reliable cost estimations, as shipping costs can be significant, especially for large manufacturing jobs. Additionally, the manufacturer’s location affects other factors like material, labor, energy, transportation, and taxes, which can vary by region. Industrial regions or countries may offer specific advantages, such as free trade agreements, express shipping options, lower material prices, or tax-free zones. Understanding financial conditions and trade regulations is vital for achieving more reliable cost estimations.
For example, Türkiye has favorable regulations to facilitate and expedite exports. Because of these regulations, manufacturing companies can ship products without additional customs processing up to a certain value.
Experience Sharing Continues as Manufacturing Notes!
Blade Precision Offers You Cost Breakdown
When you need a price analysis, we provide a detailed cost breakdown of our offers, including all aspects such as raw material, engineering, milling, turning, EDM, post-processing, shipping.
Blade Precision provides a comprehensive range of manufacturing solutions to meet diverse industry needs:
3 & 5 Axis CNC machining
Sheet metal cutting & bending
Surface finish operations
Heat treatment options
Contact us today for a quote! info@bladeprecision.com
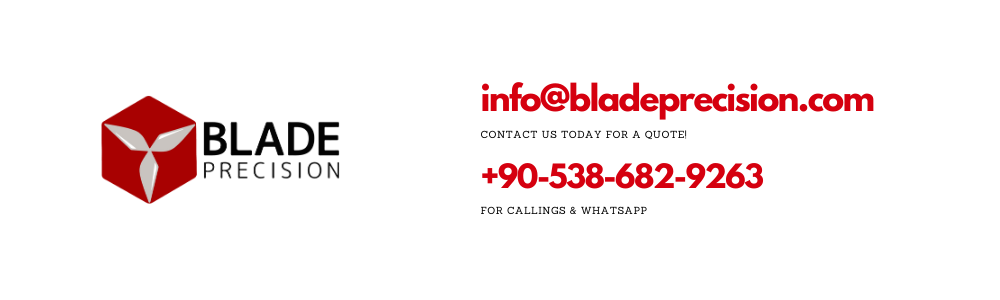